Handloom Ikat
Clothing contributes over 8 percent of all greenhouse gases and, if things continue as is, by 2050 more than 25 percent of the entire global carbon budget will go to this one industry.
Quantis completed a study in 2018 highlighting for the first time that the process within the clothing supply chain that creates the largest carbon footprint is in fact at the mills where the fibre is spun and the yarn is woven into fabric.
It's a whopping 75% of the entire lifecycle of the garment!
So what we now know is that addressing sustainability must be done first and foremost with fabric and what energy is used to create it.
You can read the full study here : Quantis
This important study has truly answered so many questions around what is the best place to start when it comes to conscious production. Three quarters of a garments impact is in the making of the yarn and fabric!
Our affinity with ikat has always been lead by the cultural heritage, it’s importance as a strong employer in rural settings (by keeping families together in their village), the beautiful hand-made nature of the craft and of course the beauty of the fabric being woven by traditional handlooms in people’s homes where electricity is scarce or completely unavailable.
These points are not to be sneered at, however to have data on the true impact of this phase of the production of our fabric just elevates its beauty, ingenuity and craft to another realm.
We are so elated to also now offer our new collection in 100% GOTS certified organic cotton and dyed with Oeko Tek certified dyes.
To be able to offer this fabric in our collections that has such a minimal impact on the planet is truly a rewarding one.
IKAT
Pronouned ee-kat it means to tie or bind yarn. Our GOTS certified organic cotton yarn is stretched out and the design is carefully drawn across the yarn by our artisan partners in Telangana, India. Then the artisan binds the individual yarns (often with discarded inner tyre tubes) to follow the design. The yarn lengths are immersed into our Oeko Tek certified dye bath where the bound sections don’t absorb the dyes, and the process continues with new tying in a different section depending on how many colours the design has.
Once the dying phase is complete the dyed yarns are then carefully placed onto a handloom where the weaving stage begins.
The weaving co-operative we work with has 11 weaving couples + other women working on tyeing the warp to weaving, re filling the weft yarn and shuttles.
All weaving is done in the homes of the co-operative couples as such no electricity is available. Purely made by hand and human skill and energy.
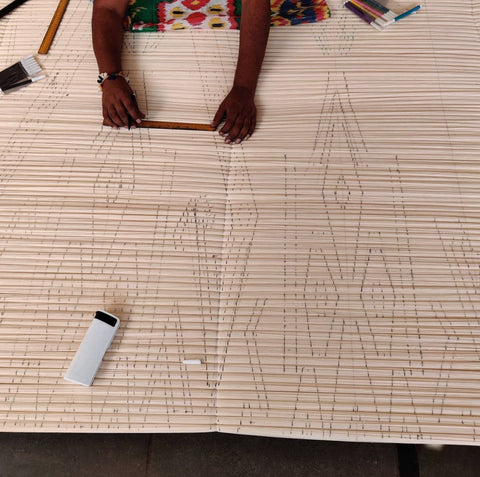


